Hot rolling and cold rolling are both steel plate or profile forming processes. They have a significant influence on the structure and properties of steel.
This article has explained the two steel processing methods used in the kitchen sink. It includes information like the difference between them and which one is best for stainless steel sinks.
Let’s get right to it!
Hot Rolling
Stainless steel hot-rolled plate is a steel plate with a thickness between 3mm and 16mm, and its surface has an industrial surface and a matte surface finished.
Both hot rolling and cold rolling are processes by which you can form steel plates or profiles. Believe it or not, the way the steel is rolled has a significant impact on the properties and steel structure.
Usually, steel has to be heated to 1100-1250 degrees for rolling. This is because billets or steel ingots are challenging to deform if it is done at room temperature. They are difficult to process if they are not heated.
This process of heating the steel for rolling is called hot rolling.
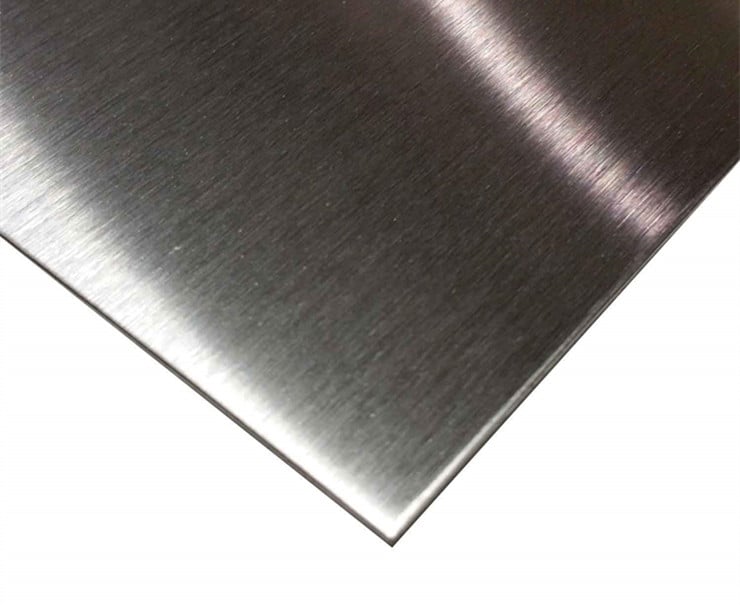
The rolling of steel is mainly hot, and cold rolling is only used to produce small section steel and thin plates.
This is higher than the recrystallization temperature for a lot of steel. It is much easier for you to form steel at such a temperature, and the products are much more convenient to produce.
The termination temperature of hot rolling is generally 800 ~ 900 ℃, and then typically cooled in the air. Hence, the hot rolling state is equivalent to normalizing.
You start with a single rectangular plate of metal called a billet to process hot-rolled steel. Firstly, you heat the billet, and then you send it for pre-processing. In this process, the billet is flattened into a large roll.
After this, the steel plate is processed through a series of rollers at a very high temperature. You repeat this process until the finished dimensions are achieved.
You spin the rolled steel into coils for sheet metal, and then you leave it to cool. For other forms of metal, such as bars or plates, you section materials and package them.
After that, the steel is left to cool. The size of the steel may reduce as steel shrinks a little when the temperature drops. This reduces the control over the final shape of hot-rolled steel. It isn’t suitable for materials with precision applications.
Most steel products are rolled by hot rolling. Due to the high temperature, the steel delivered in the hot-rolled state has a layer of iron oxide on the surface. This has specific corrosion resistance and can be stored in the open air.
However, this layer of scale also makes the surface of hot-rolled steel rough, and the size fluctuates wildly.
Therefore, steel with a smooth surface, accurate dimensions, and good mechanical properties are required. Cold-rolled semi-finished products or finished products are used as raw materials.
Advantages of Hot Rolling
●Hot rolled steel is very easy to make as compared to cold rolled steel.
● It is also cheaper than cold-rolled steel.
● It’s also free of any internal quenching, which is a pro.
Disadvantages of Hot Rolling
● The steel has slight distortions.
●May appear some dimensional imperfections.
Cold Rolling
A cold-rolled stainless steel plate is a steel plate with a thickness of 6mm or less, and the surface is 2B and bright finished.
In cold rolling, you squeeze the steel with intense pressure. This is all done at average temperatures, so it is a challenging task to do. The pressure changes the steel’s shape.

The intense pressure will slightly increase the steel’s temperature, but this process is still called cold rolling. The steel coil formed by hot rolling is sometimes used as raw material. You can remove the oxide scale by pickling so that the pressure is processed.
Cold rolling poses advantage in that the surface is smoother due to no use of heat. It is better because of pickling as well.
However, continuous cold deformation changes the shape of the steel slightly. The hardness and strength of the steel are increased due to the cold work hardening. But, at the same time, the power of the plastic index is decreased.
However, for end-use, the stamping performance of the steel deteriorates because of cold rolling. And, this end product is appropriate only for simple deformed parts.
Advantages of Cold Rolling
● The most significant advantage of cold-rolled steel is the proper shape.
● Moreover, there are more variations when it comes to cold-rolled steel, which offers a smoother surface.
Disadvantages of Cold Rolling
● The steel is more expensive at the same time.
● Also, there are relatively lesser shapes available for cold-rolled steel.
The Main Difference Between Hot Rolled And Cold Rolled Steel
One of the main differences between the two variants is the temperature at which they are processed.
When it comes to hot rolling, the steel plate is processed at very high temperatures. Cold rolling usually refers to processing done at a lower temperature, usually room temperature.
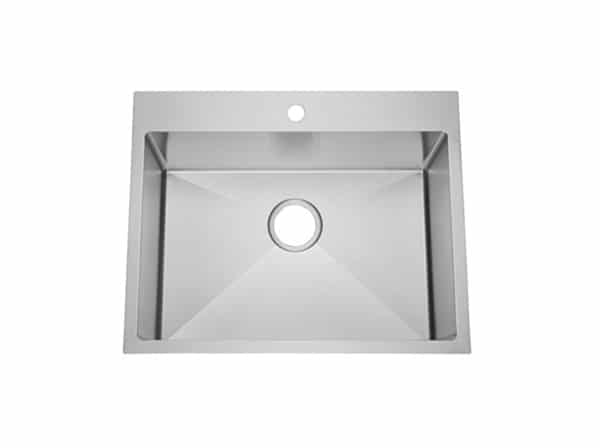
Both of these processing techniques can affect the overall performance of the steel. It also changes the potential applications of the steel plate.
Knowing which type of steel to use can significantly reduce the raw material spending and can reduce wastage.
Conclusion
Both hot-rolled and cold-rolled steel have certain advantages and disadvantages. Some of these might be clearer after knowing more about the manufacturing processes of both sheets of steel.
I hope this information helps you in deciding on which alternative to go for.
Good luck!